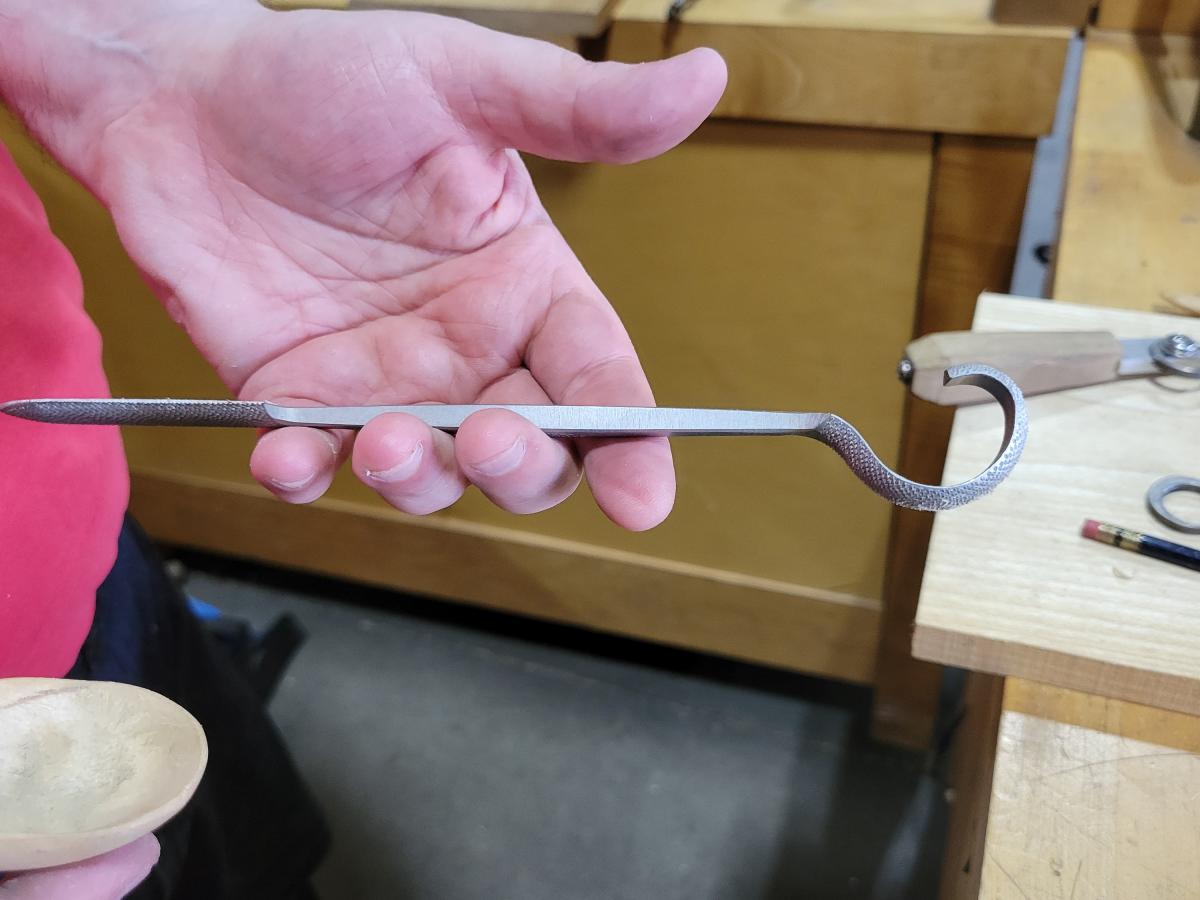
Most new tools are tweaks on old designs. A longer handle, a shorter handle, a different sized cutter. You get the idea. But sometimes - usually after a bout of frustration with our current tools - we get a new idea. This is one of those times.
I'm a big fan of rasps and an even bigger fan of hand cut rasps. The reason is they cut quickly and very smoothly. Another great reason for rasps, especially fine toothed ones, is that rasps, unlike sandpaper, don't leave abrasive grit behind. (This abrasive can dulls tools.) So it is eminently practical to do your carving and then continue on with a rasp, and then go back to using carving tools. Another advantage is the rasp's very precise, solid, cutting action. Sandpaper's precision depends on how you are holding and supporting the back of the sandpaper, and of course sandpaper really only conforms in one dimension at a time.
Some people love the crisp look of a spoon just made with knives. Others want a smoother blended look -- and that's where rasps are ideal. But most tools don't have a curve tight enough for fitting into your average spoon sized bowl. Regular traditional riffler rasps typically don't have a tight enough curve at the end. What you want is something reasonably wide, but also an in a fairly tight curve. And such a combination has not existed.
Now let's step back for a second and talk about riffler rasps. A riffler rasp is a double-ended rasp that's designed to have complementary shapes at each end. Traditionally they were made for pattern makers who would rasp away with one shape and then flip the riffler very quickly in hand for a different cutting action. We sell sets of rifflers, we sell a general purpose riffler, all of which are great and popular with carvers. But none of them have a tight enough radius to get into a small spoon bowl.
So a light bulb went off, and I thought of a riffler that can get into a bowl. What we ended up with is a spiral that gets tighter and tighter for smaller bowls, and is about 3/8 inches wide so you aren't working a groove in the bowl. We put a regular end of a cabinet maker's rasp on the flip side so you can do flats and half rounds on handles (especially at the base of a handle). Intellectually the shape made a lot of sense, although the spiral was the first new shape in riffler rasps in several lifetimes, and the rasp maker needed a lot of time to figure out how to make it. We sent drawings and even a 3D printed model, but the rasp wasn't something we could prototype. The raspmaker had to scratch his head and figure out the details of the steel blank needed when you rolled it up to get the spiral we wanted. (Not to mention the tooling needed to get a smooth spiral - that took a few tries.)
But we're pretty pleased with the result. It's a fine-toothed finishing rasp, and it won't take off a lot of material in a hurry. But it will leave a nice surface, and is great for blending, which is the whole point. You can check out more details here.
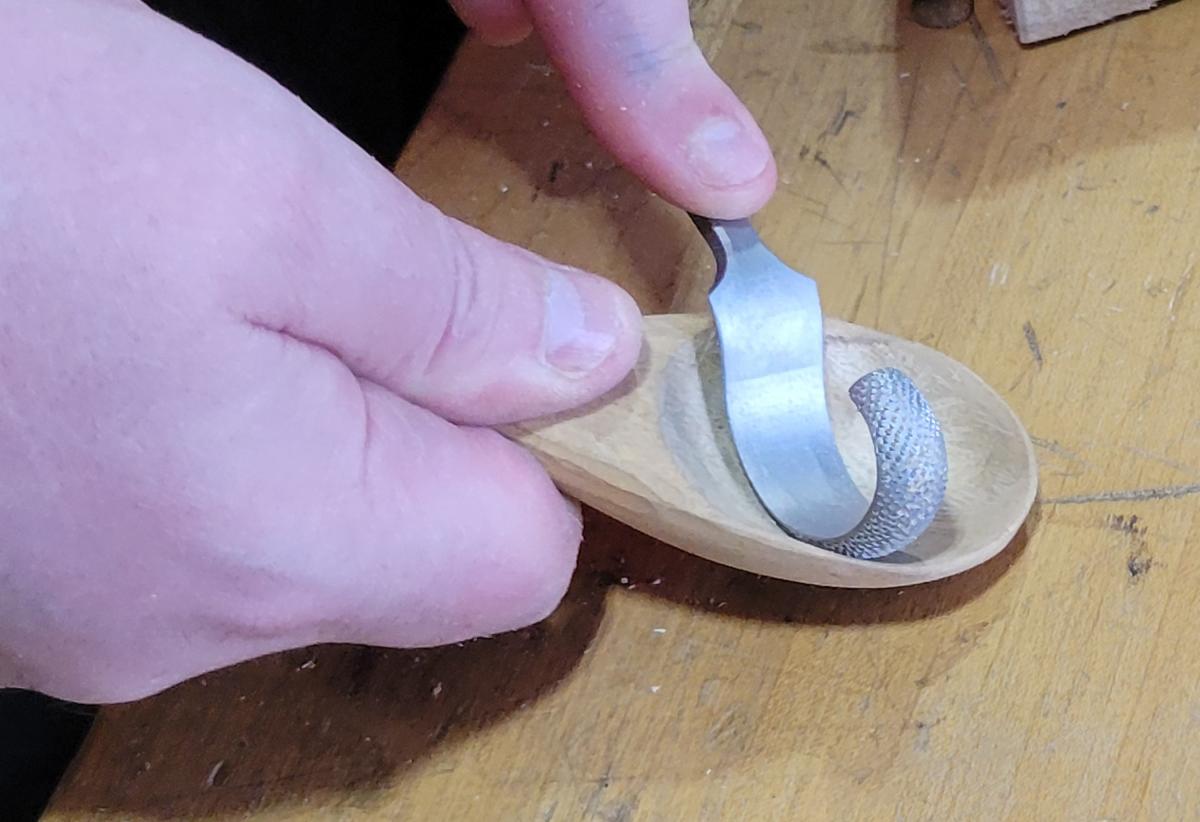
We hope you like it.
In other news, our first prototype flywheels for our lathe came from the foundry and they look really good. We're at the point of the lathe where we're figuring out production and we're getting closer and closer. Our biggest problem is that it's not like we're going to make a million of these, and a lot of companies just don't want to be bothered by small runs.
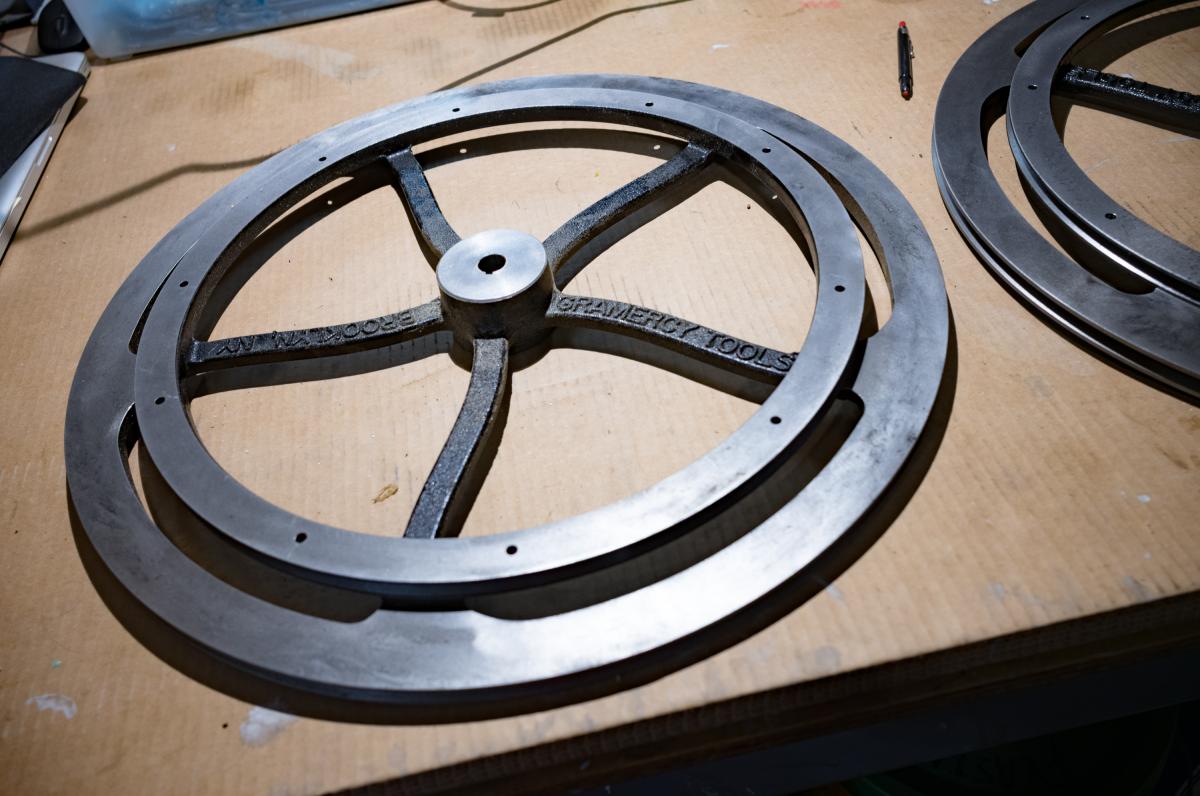
|